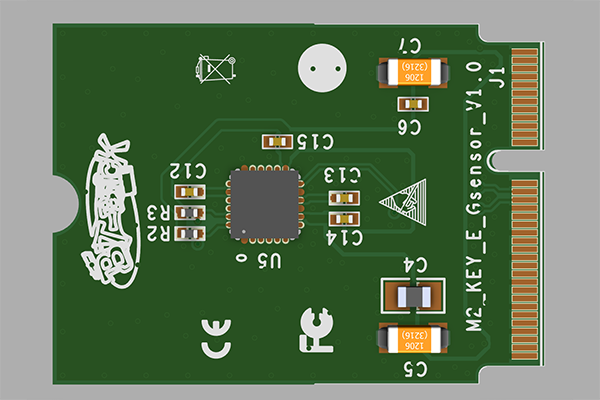
Acceleration Module
This acceleration module is specially designed for the wireless communication applications of development boards and is built with the MPU 6000 motion sensor as the core. It integrates precise sensing and efficient wireless transmission capabilities, endowing the development boards with accurate motion perception functions. It can be widely adapted to diverse fields such as the Internet of Things and smart hardware, helping devices achieve dynamic monitoring, attitude analysis and intelligent control, and becoming a powerful component for the development of innovative projects.
Function
Multi-axis Motion Perception
It integrates a 3-axis MEMS gyroscope and a 3-axis MEMS accelerometer. Through their collaborative operation, it can accurately capture the full range of motion states of objects in three-dimensional space. Whether it’s linear acceleration or deceleration movements, or rotational and tilting attitude changes, it can keenly perceive them and output the quantified results. It provides real-time feedback on motion details for the devices equipped on the development board. For example, in smart wearable devices that track human walking and running actions, it can precisely record the motion trajectories and attitude changes.
Data Fusion and Output
It has a built-in advanced digital motion processor (DMP), which can efficiently fuse and process the raw data collected from the gyroscope and the accelerometer. It can output fused data of 6 axes (3 axes of the gyroscope + 3 axes of the accelerometer) or 9 axes (which can be achieved by integrating geomagnetic data). The data covers rich formats such as rotation matrices, quaternions and Euler angles, facilitating the direct connection, analysis and utilization by the development board, enabling it to quickly grasp the attitude information of objects. It can be used for the stable attitude control of unmanned aerial vehicles (UAVs) to ensure smooth and precise flights.
Programmable Measurement Range Adaptation
In view of different degrees of motion intensity and application conditions, the measurement range of the gyroscope can be flexibly selected, covering multiple ranges such as ±250, ±500, ±1000, and ±2000 °/s. The measurement range of the accelerometer has ranges of ±2, ±4, ±8, and ±16g. Developers can program and set them as needed. For monitoring daily movements with conventional consumer electronic devices, low ranges can be selected to ensure accuracy. For monitoring the vibrations of industrial heavy machinery, high ranges can be chosen to cope with large dynamic impacts.
Efficient Data Buffering and Transmission
It is equipped with a large-capacity 1024-byte FIFO buffer, which enables the temporary storage of continuously collected data, relieves the pressure on the main processor of the development board caused by frequent interrupts for data retrieval, and reduces the overall power consumption of the system. In combination with the I2C fast mode that supports 400 kHz and the SPI interface with a maximum speed of 20 MHz, it ensures the high-speed and stable transmission of motion data to the development board, meeting the requirements of scenarios with high real-time demands, such as the real-time feedback control of robot joint movements.
Specification
- Core Sensor: MPU 6000
- Number of Measurement Axes: 3-axis gyroscope + 3-axis accelerometer (expandable to 9-axis integrated output)
- Measurement Range of Gyroscope: ±250, ±500, ±1000, ±2000°/second
- Measurement Range of Accelerometer: ±2, ±4, ±8, ±16g
- FIFO Buffer Capacity: 1024 bytes
- Interface Types: I2C fast mode at 400kHz, SPI (up to 20MHz)
- Operating Temperature: -40 ~ 85 °C